Tuples’ use cases – AIRBUS manufacturing, planning transport and resources
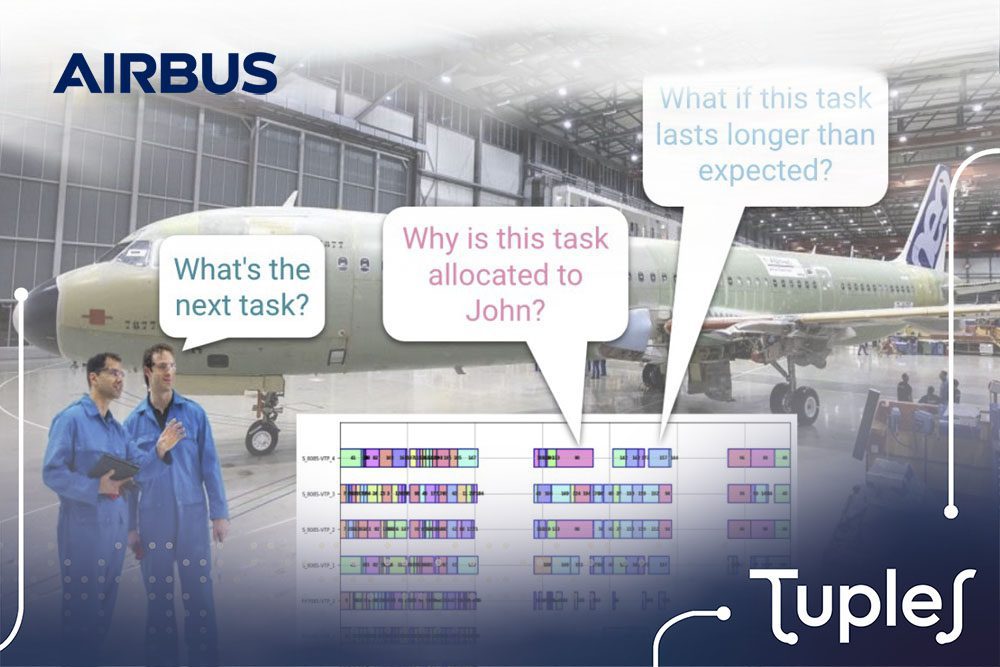
One of the main activities in the first year of the project has consisted in consolidating and formally defining the use cases provided by the industrial partners of the project.
They come from all the industrial partners of the project and cover the different research fields of the project in terms of trustworthiness (verification, explainability, robustness) and hybridisation (between data-driven and model-based approaches to decision-making):
– 2 use cases from Airbus: one on manufacturing optimisation and the other on flight diversion management;
– 2 use cases from Optit: one on energy management and the other on waste collection optimisation ;
– 1 use case from SciSports on football squad management.
Airbus Manufacturing: Planning transports and resources
The manufacturing use case is based on well-known scheduling and resource allocation and planning challenges and this use case has a number of special features that make the challenge much more complex. The use case has two applications: robust scheduling of resources and resource allocation for rack systems.
In the first application, resources (workers) are assigned to tasks to create a work schedule. Currently this process is done by two teams of planning technicians using a web based app. The app disallows double assignment. These planning technicians assign similar tasks to the same workers in order to minimize logistic costs (continuity). Disruptions happen in real time, modifying the availability of resources. In these events, it is very difficult for the planners to adjust the schedule in an optimal way. Also, conclusions about feasibility, resources and decision is desired.
The team is asking for an autonomous method to optimise schedule generation and enable rescheduling under disruption, maximizing lead times and continuity.
As a first approach to the desired solution, or “first phase”, a schedule without worker allocation where the challenge consists in assigning workers to the scheduled tasks, taking into account working hours, skills needed and work balance constraints, as well as the cost of a worker moving from the location of their current task to the location of their next allocated task. Then, once the challenge is solved, a more complete approach, or “second phase”, will be explored to schedule tasks in addition to allocating workers to them, considering task preemption and time-based precedence relations in addition to the previous constraints.
The second challenge addresses storage and management of cargo transported by Beluga™ aircraft, bringing aircraft parts that need to be inserted in a rack system that also works as a multi-queue system.
Here the challenge is to decide which rack is allocated when a part arrives or must be sent to the factory to minimize effort (number of movements), space use (in the racks), and delivery delays (to the plant). These decisions are based on different optimization parameters like time, space allocation, etc.
Trustworthiness questions:
Why has this task been put in this order?
What are the most important constraints for this task/schedule?
What would happen if the schedule is modified?
What is the difference between using an option or constraint when generating the schedule?
How was the movement chosen?
If the next scheduled flight gets delayed or arrives sooner what action should be taken?
What is the expected final state / position of the racks or the jigs?
Objectives
The objective for scheduling of manufacturing resources is to minimize the distance traveled by the workers between assigned tasks and also to balance the workload between the teams. For Beluga ™ logistics planning, we want to optimize different parameters such as time, space and rack usage, and also to obtain multiple solutions for different combinations.
In both cases, response times requirements vary depending on the urgency: 1 minute for emergencies, 10 minutes for replanning under disruption, and overnight to compute schedule in non-urgent situations.
Uncertainties and robustness
Uncertainties concern Beluga™ flight times, which may be delayed or canceled due to weather conditions, or non-readiness of the incoming aircraft part, and aircraft part demands from the final assembly line (uncertainty on when the different parts stored in the racks will be need to be unloaded from the racks).
Explainability
Concerning the scheduling of manufacturing resources, planning engineers want to understand the feasibility of schedules, rescheduling decisions, and importance of – or showstoppers for – tasks and resources.
Concerning Beluga™ logistics planning, planning engineers want to understand about the state of the racks, rack selection decisions, showing alternative solutions, and optimization parameters tradeoff.